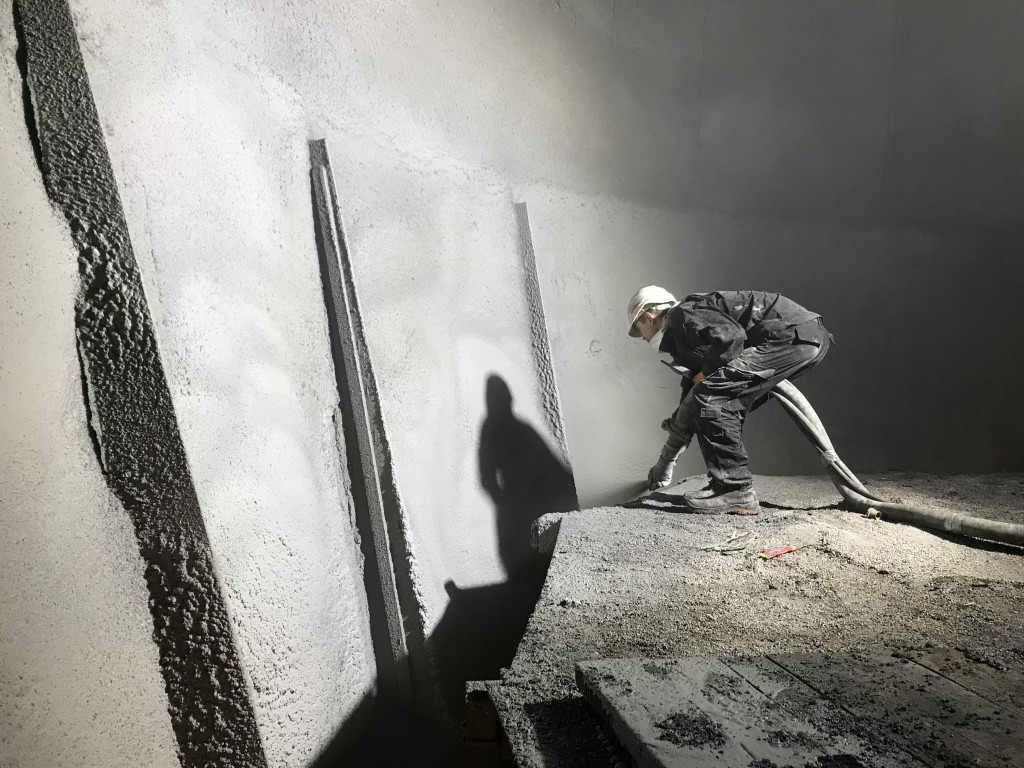
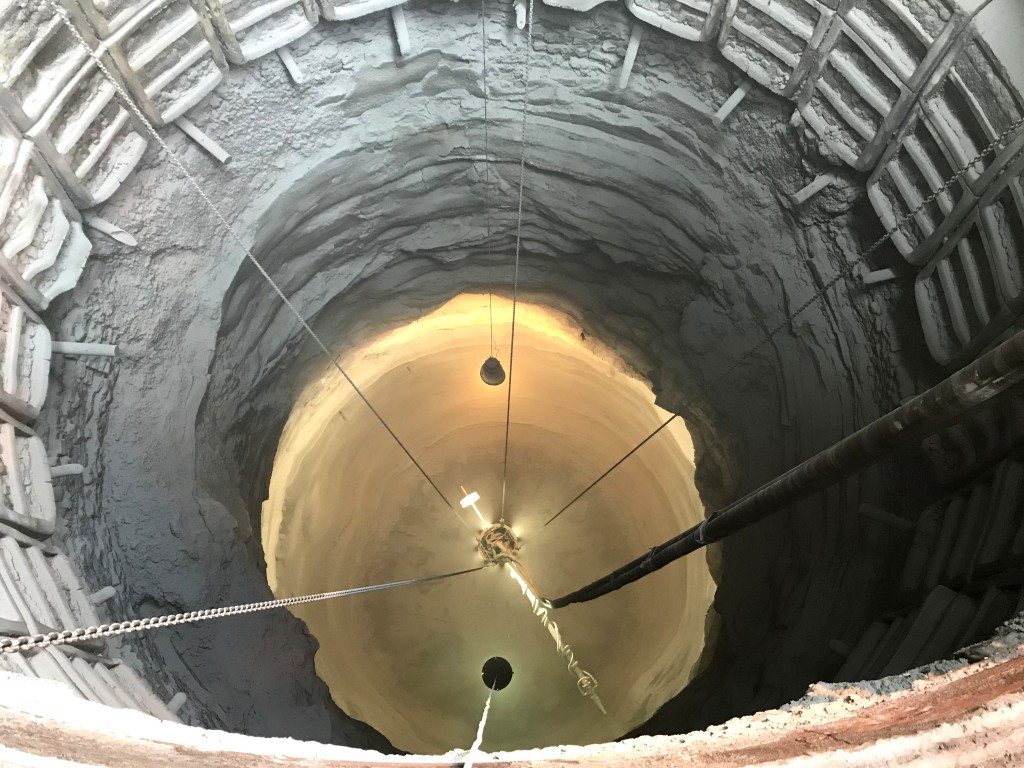
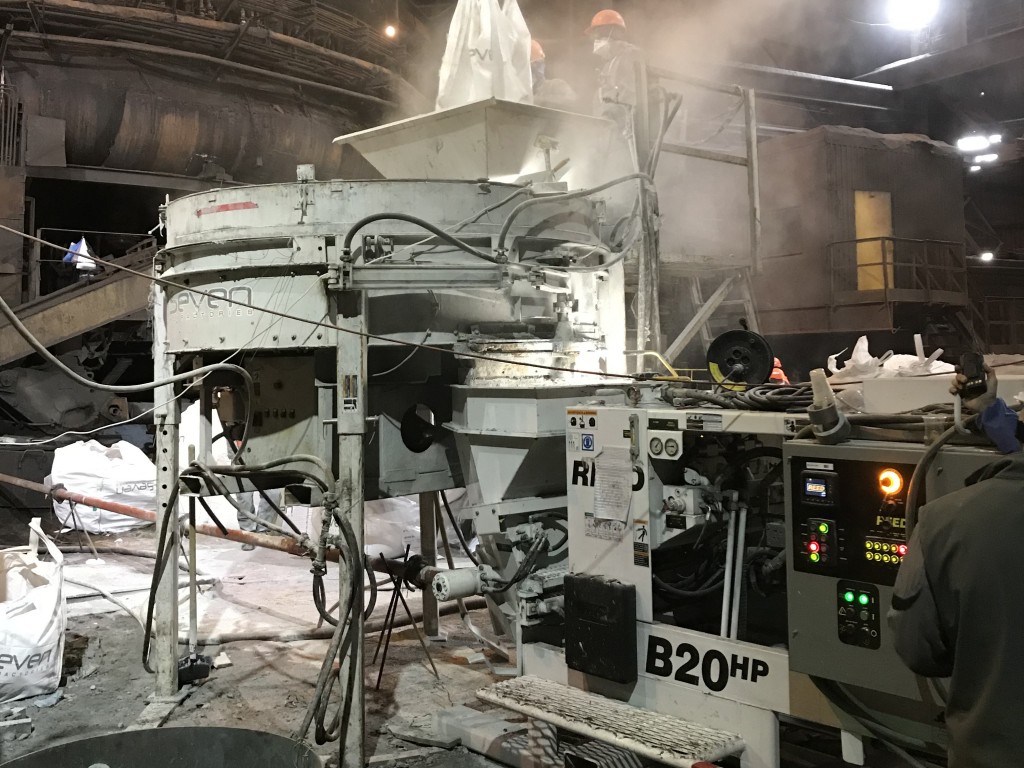
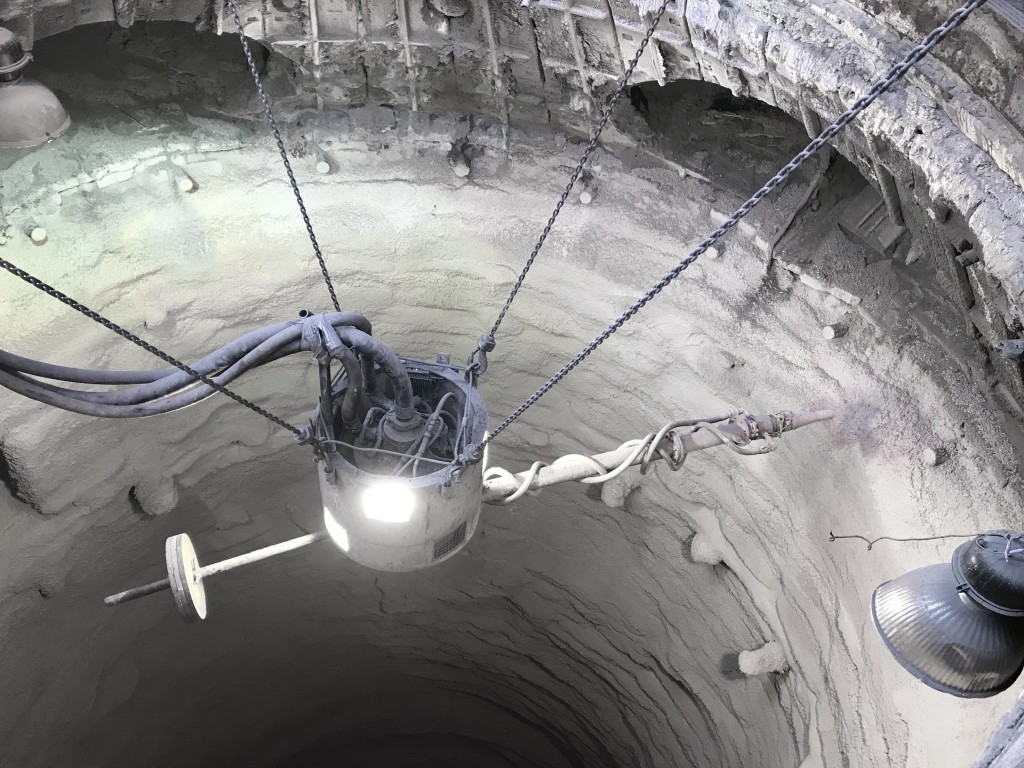
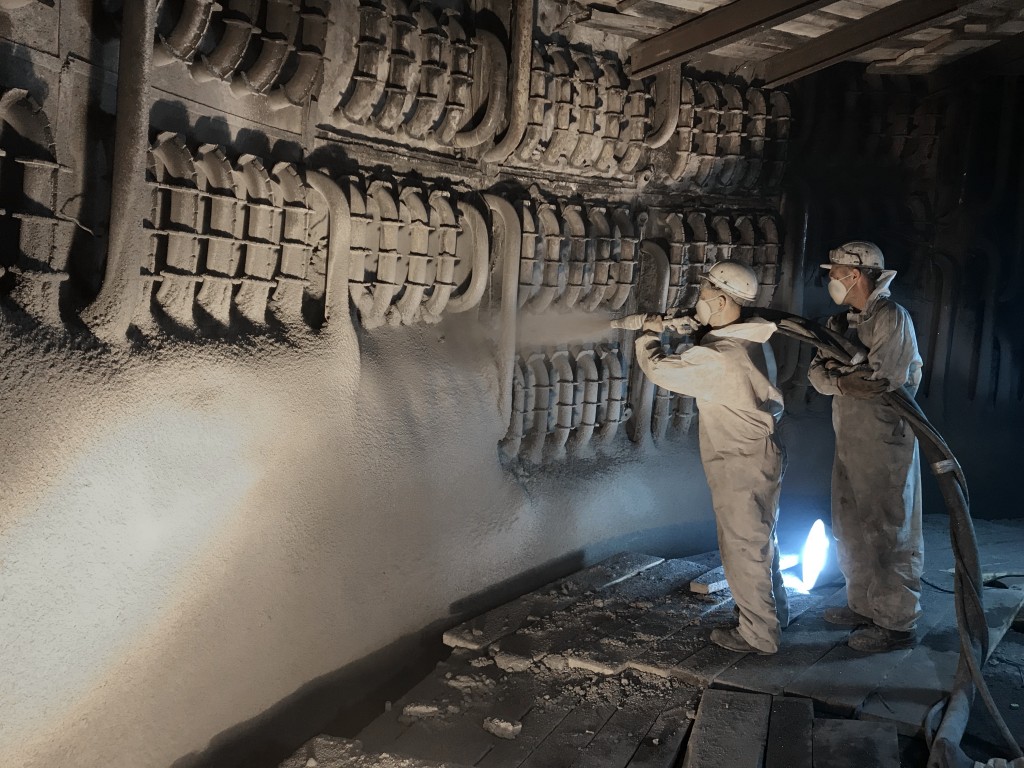
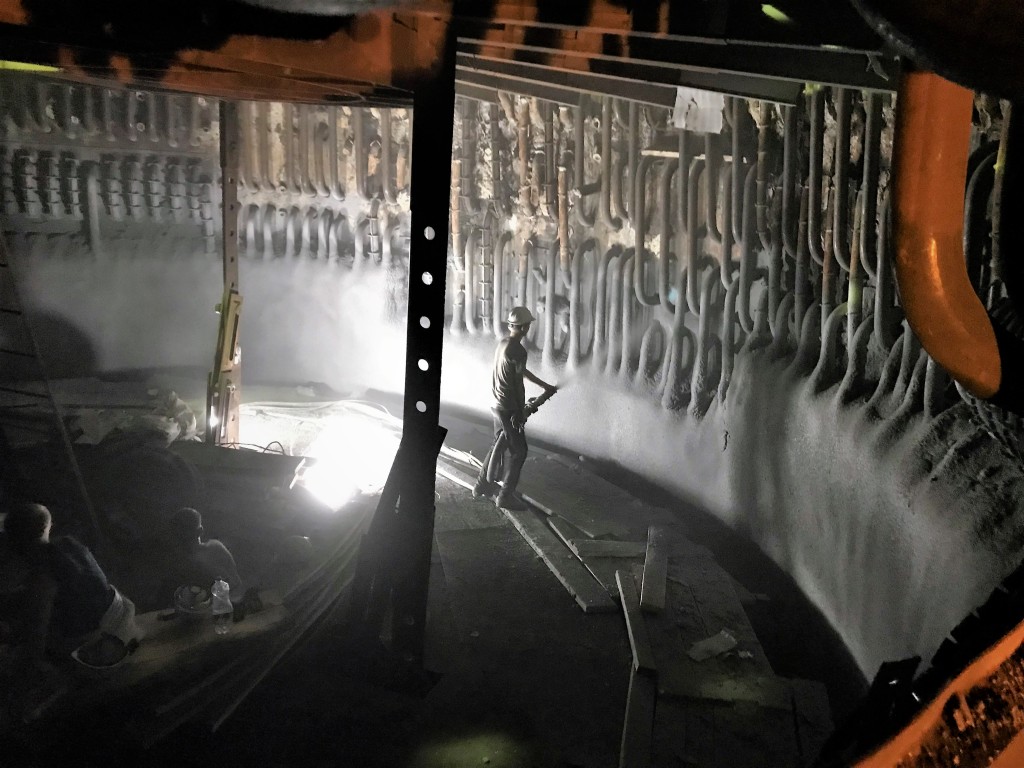
Based on a large product portfolio of refractories, We offer the most integrated approach to blast furnace repairs.
Blast furnaces have been at the core of our activities with more than 60 successfully completed projects world-wide in only 10 years. The most comprehensive repair to date included the hearth, the shaft, the gas up-takes, and the cyclone.
The Modular Hearth Shield (MHS) offers products to create a protective long lasting layer for the carbon lining in the blast furnace hearth.
With this concept we offer an ideal geometrical solution based on optimal material quality, instead of liningfollowing a “just enough” approach.
Carbon lining protection, i.e. contrast the erosion mechanisms given by:
Ready-to-use block shapes prevent hot metal from floating out and the improved heat-transfer to the cooling elements contributes to the formation of a dense protective layer at the MHS surface that preserves the blocks from further consumption, thus enabling them to exploit their proper technical function.
All in all, the MHS solution leads to several years of life expectance and therefore cost savings.
A refractory model designed to optimize the whole of hearth lining, block shapes, quality zoning distribution, thermo-mechanical stresses.
A pre-assembled solution allows:
All blocks are engineered on white fused alumina and/or fused alumina – mullite; the ramming is engineered on brown fused alumina – Carbon – SiC; the mortar is engineered on brown fused alumina-bauxite.
Material quality and geometrical solution overcome the concept “preshaped” lining.